When planning your robot welding cell configuration, there are several critical factors to take into account to ensure optimal performance and return on investment. The right setup depends heavily on your specific manufacturing processes and production goals.
Standard systems offer budget-friendly, pre-engineered solutions designed to handle various component sizes and welding tasks, providing a quick return on investment. In contrast, custom systems are tailored to meet unique manufacturing needs, address specific welding challenges and optimise production output.
Key considerations include process requirements, component size, welding specifics, and safety and accessibility. Proper layout planning is essential to ensure efficient and scalable operations.
- Process Requirements: Identify what you aim to achieve by automating your welding process. Are you looking to increase throughput, improve weld quality, or reduce labor costs? Process requirements include how operators and robots interact, and how tasks are sequenced.
- Component Size and Type: Determine whether you are dealing with small or large components and if they require orienteering. This will influence the size and type of welding cell you need as ensuring the robot can reach all necessary weld points on the part is crucial for efficiency.
- Welding Needs and Details: Consider the nature of the welding tasks, whether they involve small or heavy disposition welding. The type of welding, weld locations, access points, and the number and complexity of welds all influence the layout.
- Safety and Accessibility: Ensuring adequate space for safe operation, proper guarding, and easy access for maintenance and future expansion is essential.
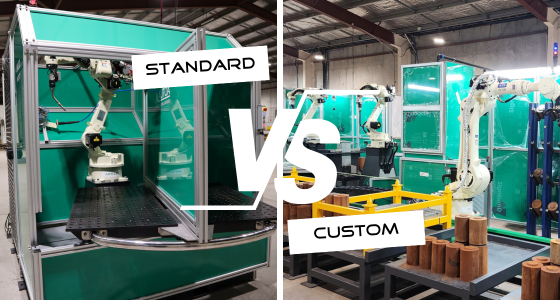
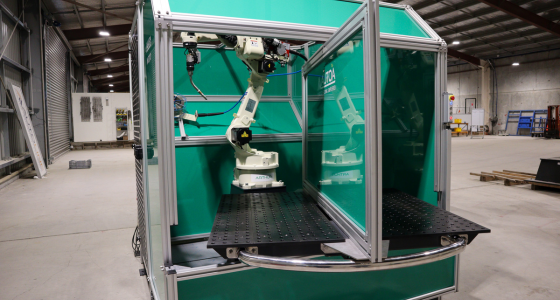
Standard robot welding cell configurations.
Customised Robotic WElding Configurations.
Our customized robotic welding solutions are specifically designed to meet your unique requirements, providing a competitive edge by optimizing your production output. We develop custom solutions for various specific welding needs, including hydraulic cylinder welding, automated tube welding, and custom workpiece positioners. Our expertise extends to addressing the unique and complex challenges of your processes, ensuring precise and consistent results. Whether it’s the type of welding or a specific process unique to your manufacturing needs, we have the expertise to help design and integrate a custom robot welding solution.
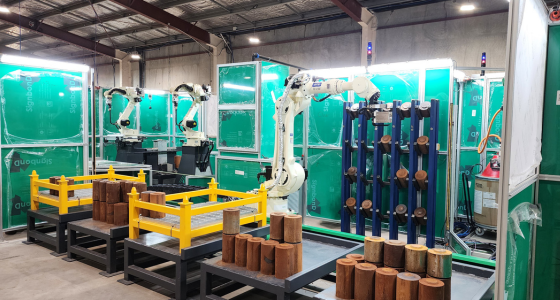
Seamless integration and peak efficiency
Both our standard and customized solutions are designed to operate at peak efficiency, minimizing downtime and maximizing output. From initial planning to execution, every aspect of the system design is tailored to ensure that your operations run seamlessly and effectively. These tailored solutions help you achieve your production goals and maintain a competitive edge in your industry.
With both our standard and customized robotic welding solutions, you can be confident that your manufacturing process will be optimized for maximum productivity and efficiency.